Share this
At the start of the new year, Hayes Brakes took a significant step forward by enhancing their 3D printing capabilities with state-of-the-art technology. This strategic decision was made to further enhance their product development process, enabling them to be even more agile in creating innovative solutions on tight timelines. With the addition of in-house printing capabilities, Hayes now has a comprehensive range of 3D printing resources at their fingertips.
Nathan Zinser, a test engineer at Hayes, explained how this advancement will streamline their internal processes and ensure that Hayes continues to deliver top-quality products and unparalleled service to their valued customers.
Nathan, you were part of the team that led the initiative to bring 3D technology in house. Can you explain how your cross-functional team arrived at that decision?
Frequently customers want to see parts as soon as possible, so getting actual, physical working parts to them sooner is key. Having a highly capable 3D printer in-house will help us do that. We can go from an early engineering development phase to our first hard tool parts that will work and function with far more confidence.
In prior years, the Milwaukee School of Engineering (MSOE) Rapid Prototyping Consortium has been our primary resource for additive prototyping. The consortium had introduced us to Stratasys as a printer supplier. Stratasys printers boast an exceptionally user-friendly interface, heavily featured in a lot of the ways that we're looking for, as well as being a professional grade piece of equipment able to satisfy most of our needs.
I see the technology as an opportunity to iterate quickly as an organization, speed along our product development, develop better visual aids for ourselves, and provide customers with proven product faster.
I've already seen this printer being used in that way. Last week one of our design engineers printed torque takeout brackets on the 3D printer and now we're already talking to ACI Industries, Hayes’ own machining house. That rapid development is due to the fact that we've already proven the design with the 3D printer.
How will this technology benefit Hayes’ capabilities?
A cross-functional team brought the value of in-house 3D printing to light last year and the company acted quickly to take advantage of the opportunities identified. The immediate benefit to Hayes and, most importantly, our customers is the early testing and validation we can deploy in product design and development. The printed parts allow us to learn earlier, iterate quickly, and have the best design confidence when going into product development.
In the first few weeks here, we've seen it used all through product development as well on the manufacturing floor and direct end-use fixturing, so there's function there. You just have to understand that they are plastic and limited in some of their capabilities.
That said, there's certainly opportunities to demonstrate function with the parts, but mostly utilized as a proof of concept or visualization in a prototype landscape.
Will Hayes continue their partnership with Milwaukee School of Engineering?
The MSOE 3D Printing Consortium continues to offer cutting edge and niche technologies for us that we would not be justified to bring in-house at this time. So, what we did is only brought in the core - or the most heavy-use type of technology - while maintaining our partnership with the MSOE RPC for those prototyping activities demanding more specialized equipment.
It sounds like this will allow Hayes to be more agile with product; explain how precise the model samples are.
We recently had some fixturing that went from idea generation in a quick little brainstorming design review to actual parts and in service, in less than 24 hours. I should note that the parts cost us about $10 in material to print, keeping costs down for customers and builds on schedule while rectifying a sporadic assembly issue.
Because of the accuracy of this printer and its use of dissolvable support material, no additional design effort is needed to “design for additive” here. We can take our designs directly from CAD to the printer. With other printers you might have to modify the way that you're designing just because of the printer’s limitations, but not in this case. Having this equipment under our own roof allows us to work very quickly.
Additionally, the materials Hayes can print in offer a broad spectrum for testing. We typically print with plastics, but we also have flexibles and some carbon fiber reinforced composites that are available as well. These materials are tough, durable, and strength capable.
Having advanced testing equipment and 3D printing capabilities in-house and readily available to our engineers is just one way Hayes chooses to serve customers and commit to their need for speed. To learn more about working with Hayes and our history in braking innovation, reach out today.
Subscribe to our blog!
Related blogs
Section Intro
Help visitors get the basic idea within a few seconds, so they understand what this section is about.
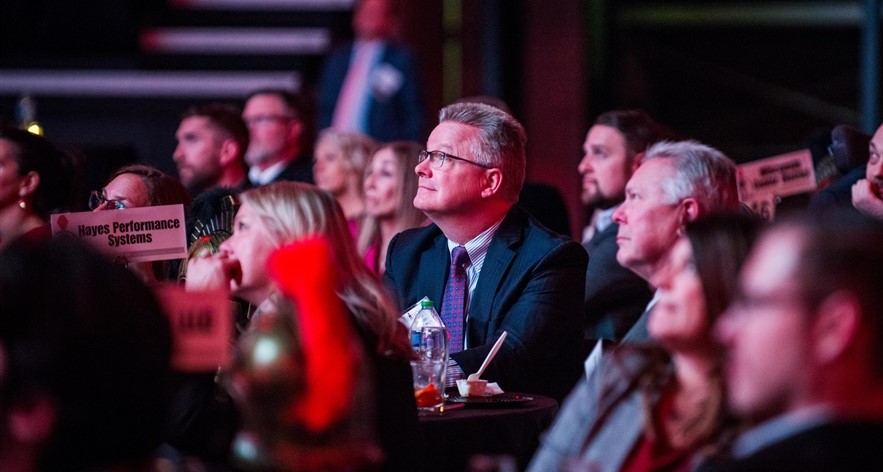
Hayes CEO Honored as Industry Titan
Hayes Performance Systems is pleased to announce that, for a second year in a row, CEO & President Phil Malliet has been recognized by Titan 100 as one of the 100 notable executives in Wisconsin. The...
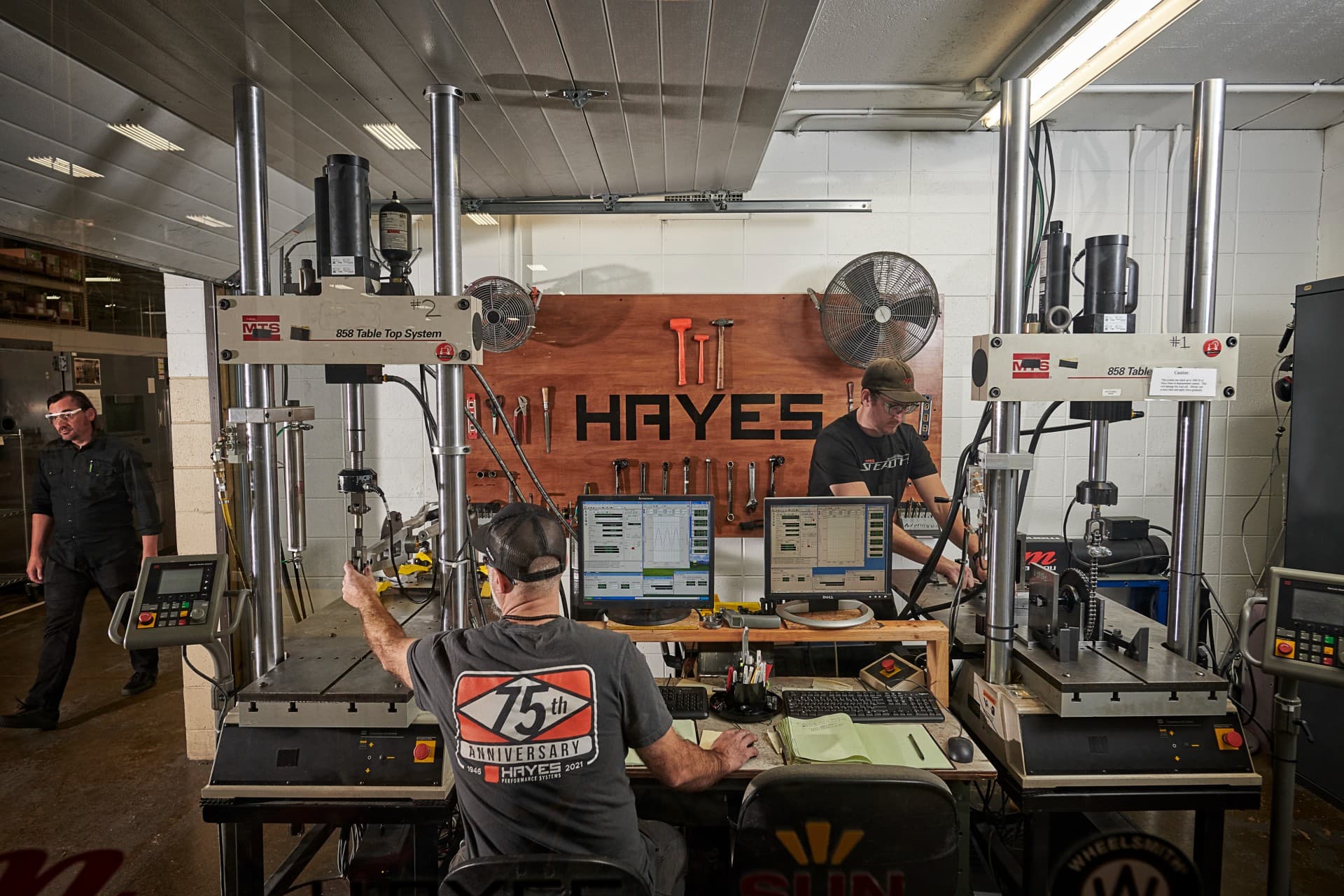
The Future of Braking: Why Expertise Matters in Integrating Advanced Electronics
Fortunately for today’s drivers and passengers, significant advancements have been made to improve vehicle safety, stability, and performance. Some of the most notable improvements include anti-lock...
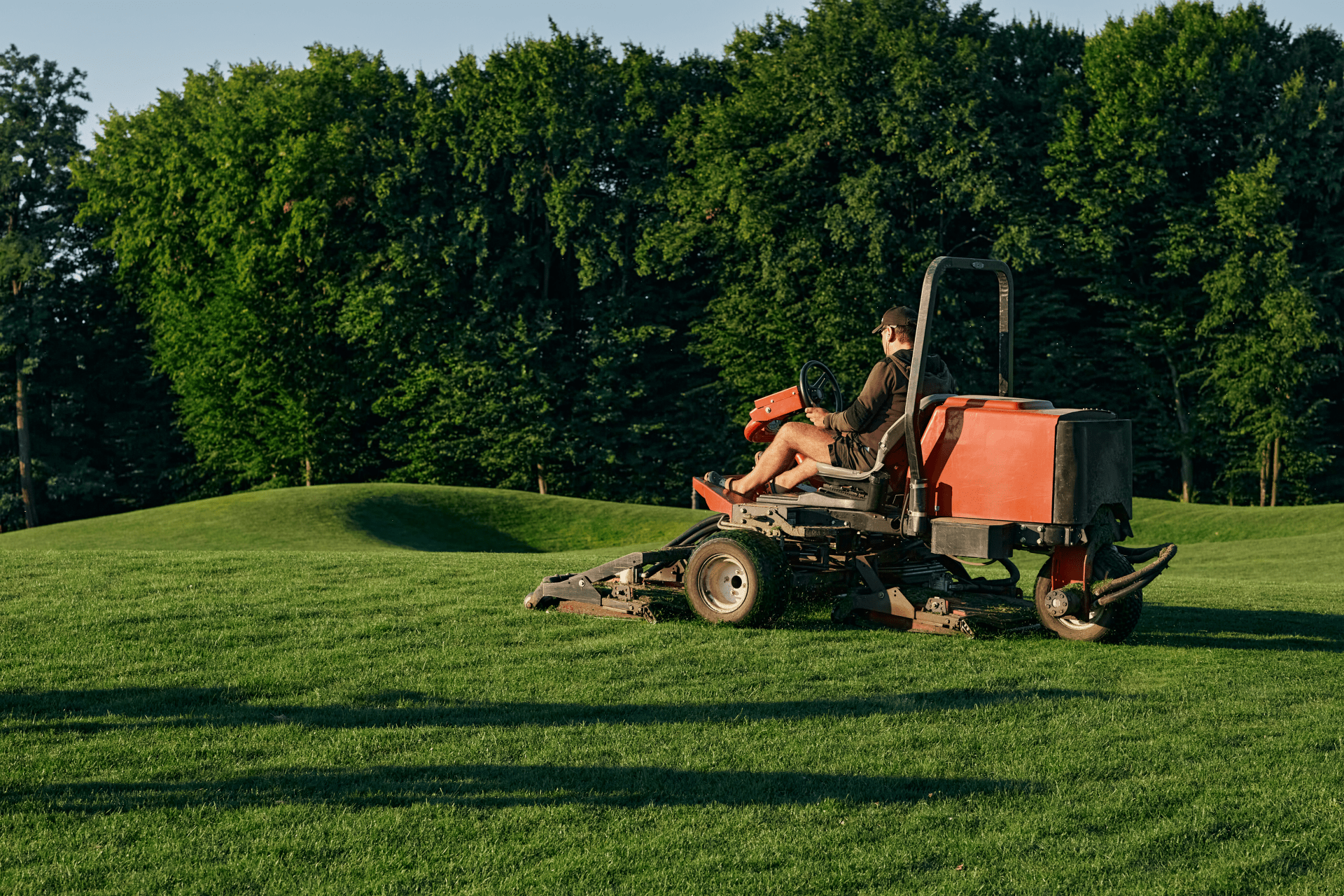
Collaborative Product Development: How Customized Brake Solutions Give OEMs an Edge
Here’s a team-up that seems out of left field: John Deere and … NASA?
It’s true: John Deere collaborated with NASA’s Jet Propulsion Laboratory to create a GPS system that makes self-driving tractors...