How to Improve Disc Brake Performance in Muddy Conditions
Share this
Tractors, plows, cultivators, and other agriculture vehicles perform critical work while driving on mud that can damage sensitive equipment.
Higher ground clearance helps other components, but working parts closer to the ground are at greater risk. Disc brakes are especially susceptible. Mud is abrasive and can easily splash and cake onto intricate brake components. Rotors and pads wind up scuffed and scratched, especially when the mud dries to more abrasive dirt and rocks.
The part damage is costly, and extremely muddy conditions affect overall brake performance — creating significant safety hazards.
Here are four ways to improve disc brake performance in muddy conditions and protect your brakes from premature wear and tear:
- Regular cleaning & maintenance
- Pairing brakes with the right tires & other equipment
- Practicing safe driving habits
- Allowing brake cooling & downtime
1. Regular Cleaning & Maintenance
For vehicles regularly driven in the muddiest farms and fields, check the brakes daily. That may add time to the work day, but it also adds time to the brakes’ lifecycle. For vehicles that aren’t subjected to the worst of the wet soil, checking at least weekly or every other day is still advised.
To clean disc brakes, operators can first remove mud or dirt by hand or with a tool or brush — gently and while carefully avoiding damaging the brakes or injuring themselves. Then, hose the mud off with a gentle spray — do NOT use a pressure washer, which could damage the brakes. Dry with a cloth to prevent rust.
Take this time to inspect the brake components, too. Look for cracks, loose connections, and other degradation. Replace parts on their recommended schedule or, if damaged, as needed.
2. Pairing Brakes with the Right Tires & Other Equipment
Pairing brakes with complementary parts maximizes performance.
Drivers can let tires with excellent traction do the hard work. That way, they aren’t constantly spinning the wheels and pressing the brakes to maintain control. Select tires for your vehicles that you know can handle sloppy surfaces.
Since brakes are one part of a system, it’s important that they fit with everything else: the pedals, brake levers, position related to the driver. Even mud deflectors, as long as they don’t contribute to overheating or other concerns. Such coordination of components happens when designing the vehicle, well before production and operation, and that’s why it’s crucial to plan for successful braking systems early on (more on that in a minute).
3. Practicing Safe Driving Habits
We can’t forget the human element.
Operators support brake performance by driving slower in slippery conditions so they’re not forced to constantly press the brakes, which could lead to premature and excessive wear and tear.
Driving on mud also increases stopping time and distances, so multiple vehicles shouldn’t follow each other too closely. All drivers should be on alert and ready to stop suddenly. With well-maintained brakes, that won’t be a problem.
4. Allowing Brake Cooling & Downtime
Muddy conditions could mean more braking than usual, maybe even riding the brake, though that should be avoided. Consistent friction generates a lot of heat, and too much heat damages the brakes — especially the brake pads.
Be sure agriculture equipment brakes are given enough cooling time and rest on some of the messiest days.
The Right Braking Systems from Hayes
At Hayes, we know brakes. We know heavy equipment. We know the ag industry. For decades, our expert engineers have made brakes for these vehicles that perform at a consistently high level.
The optimal time to incorporate custom brakes is during the vehicle design process. When you bring the team in during the design phase, you’re setting yourself up for a comprehensive vehicle and braking system that will excel, rain or shine.
Contact us today to discuss braking solutions that optimize your vehicles at every turn.
Subscribe to our blog!
Related blogs
Section Intro
Help visitors get the basic idea within a few seconds, so they understand what this section is about.
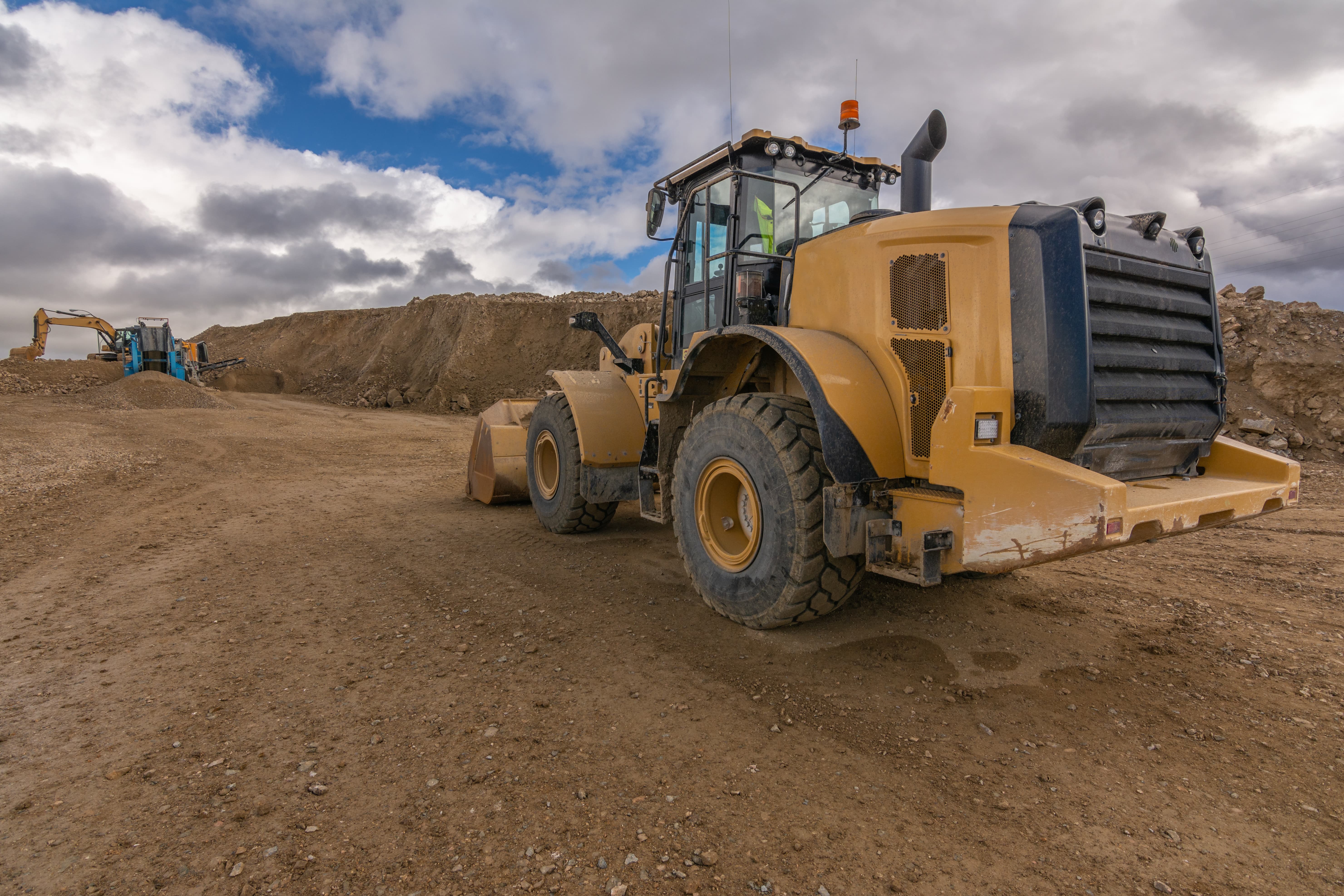
Spring Applied Hydraulic Release Brake Actuator: 4 Benefits for the Construction Industry
In 1990, Hayes Performance Systems patented its Spring Applied Hydraulic Release, or SAHR, brake actuator (initially called the Spring Applied/Pressure Release Emergency Brake Actuator) as a...
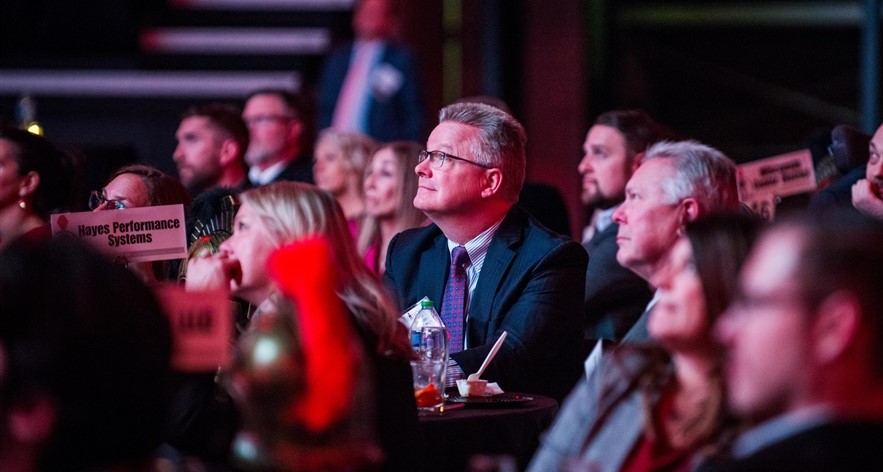
Hayes CEO Honored as Industry Titan
Hayes Performance Systems is pleased to announce that, for a second year in a row, CEO & President Phil Malliet has been recognized by Titan 100 as one of the 100 notable executives in Wisconsin. The...
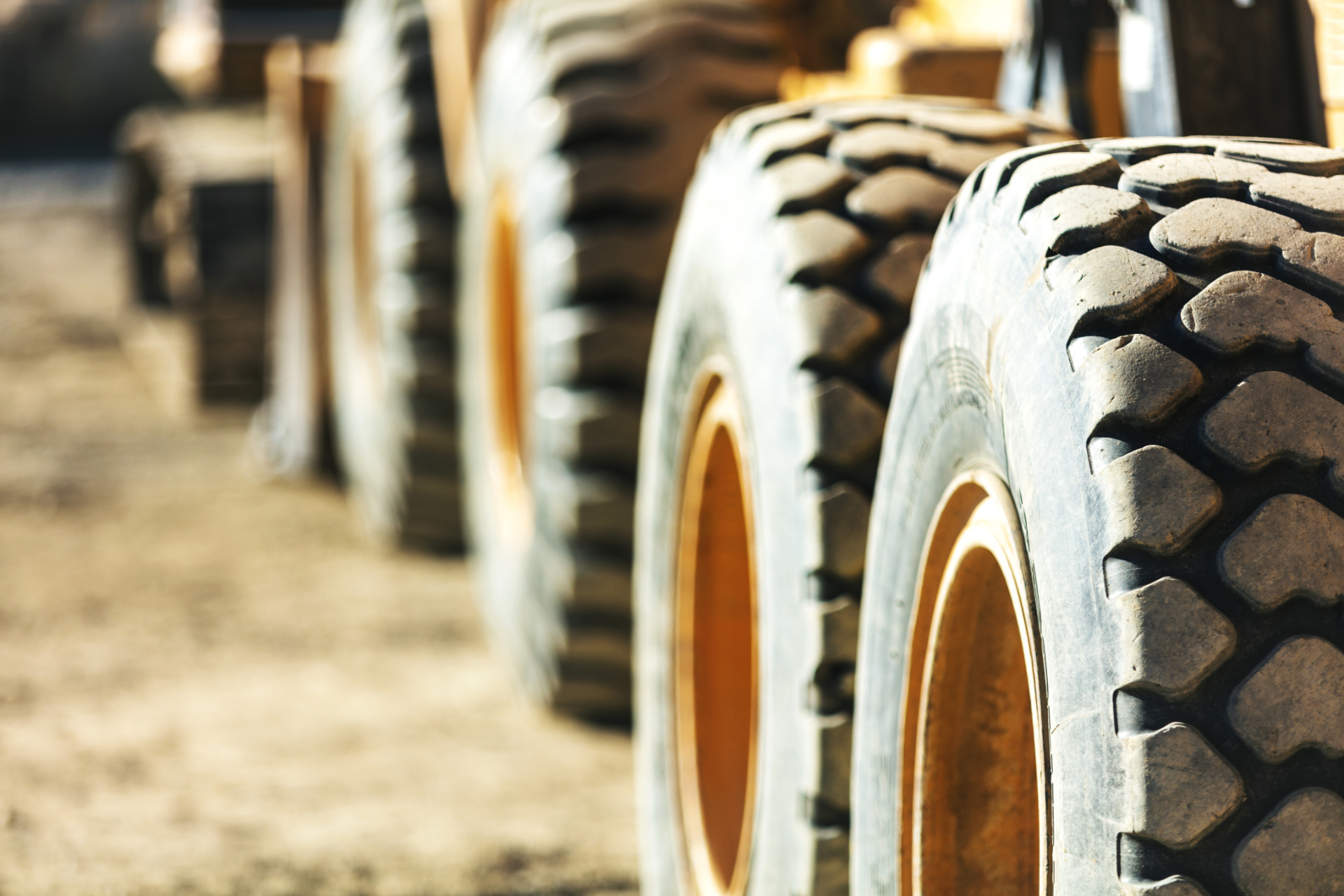
The Importance of a Construction Brake System Inspection
Heavy equipment brakes — particularly in the construction industry — are critical to instantaneously stopping massive amounts of weight and momentum. In a best-case scenario, brake failure can result...