How Powersports Brakes Manufacturers Can Meet Extreme Demands in Performance
Share this
For snowmobile riders, UTV enthusiasts, and anyone else hitting the trails, the U.S. has its share of extremes in weather and terrain — and they’re some of the biggest challenges powersports vehicles face.
How can you and your powersports brakes manufacturing partner ensure exceptional performance for your customers in those unrelenting environments?
Ruggedizing for Every Extreme
Building for extremes comes down to three critical areas: The right materials, tailored engineering, and structural analysis and testing.
The Right Materials
Around the world, riders experience an incredible variety of climates and terrains. The keys to achieving superior braking performance — temperature and shock resistance — start with choosing the right materials for the conditions and challenges.
Temperature Resistance
Using material compositions that won’t freeze and crack in bitter cold, or overheat and warp in extreme heat, is paramount. Sintered metal is ideal for both climate extremes, since ceramic composites and carbon-carbon composites withstand heat but may provide underwhelming performance in colder temperatures.
But this isn’t just about environmental temperatures; the heavy use these vehicles experience puts a massive strain on the brakes, meaning intense friction and high heat may occur from the pads and rotors. Even snowmobile brakes that routinely work in below freezing conditions must handle the effects of hot temperatures.
Controlled descents from steep slopes require an action that’s often frowned upon in other scenarios: riding the brakes. Their metal — and mettle — will face a gauntlet of continual, forceful pumping. Brake pads must be thick enough and made of heat-tolerant materials to reliably withstand non-stop friction.
And, if the vehicle design allows for the space, larger brake rotors often dissipate more heat than smaller ones to allow for increased use before getting too hot. Depending on the overall size needs, this is another avenue to explore.
Shock Resistance
No matter the location, whether it’s the Rocky Mountains or just a rocky hill, riders will likely find plenty of bumpy, twisty terrain. Brakes must be strong enough to withstand sudden stops, prolonged braking, and rough landings from riding over small ledges.
Aluminum or steel calipers hold firm when experiencing shock. Dual pistons in those calipers help with even pressure distribution. Picking the right shock-resistant materials is crucial, or nothing else matters.
Tailored Engineering
Piecing the resistant materials together in ways that allow for smooth operation in any climate requires thinking of the vehicle itself and its relation to the operator.
On snowmobiles, for instance, many riders traverse the powder with one finger constantly on the brake lever. The lever must be installed in a comfortable position, or the rider must be given the ability to adjust it (common for most snowmobilers) for easy access and use on every turn.
Other considerations include adjusting the clearance between brake pads and rotors to prevent overheating, or including rubber dampeners and pushrods to prevent excessive vibration.
Splashing through puddles and kicking up snow comes with the territory for many powersports vehicles. Mud, dirt, rocks — all those potential contaminants can get inside the brake systems and wreak havoc. Even riding in humid climates affects brake materials, with condensation and moisture slipping into open, unshielded areas.
To protect the most sensitive components, brake systems can be fully or partially enclosed in resistance material. But any enclosure must be designed with the entire vehicle in mind, making sure it will only add minimal weight and won’t hinder aerodynamic performance.
Structural Analysis and Testing
You have the materials and you have the build all set. It’s time to test!
Hydraulic shaker tables, dynamometer, and thermal shock testing are ways powersports brakes can be tested inside the facilities. But we are also strong proponents of field testing whenever possible for a more true-to-life assessment.
Since not all geographies foster ideal conditions for the real-world testing of every kind of powersports vehicle, it’s important to conduct several different types of tests — field or lab — to get the best, most conclusive results.
Read More: Dry Disc Brakes vs. Wet Disc Brakes
Talk to Hayes
The Hayes team lives for this.
When you combine extensive knowledge and experience in brake engineering with a passion for powersports, you get a group of innovators eager to take on any challenge and find ways to boost performance. We know the materials and the techniques, and we love taking our brakes out for a beautiful day of field testing any chance we get.
We’d love to discuss all things powersports and hear what you have in mind for your latest vehicles — and how we can equip them with brakes that perform. Contact us today.
Subscribe to our blog!
Related blogs
Section Intro
Help visitors get the basic idea within a few seconds, so they understand what this section is about.
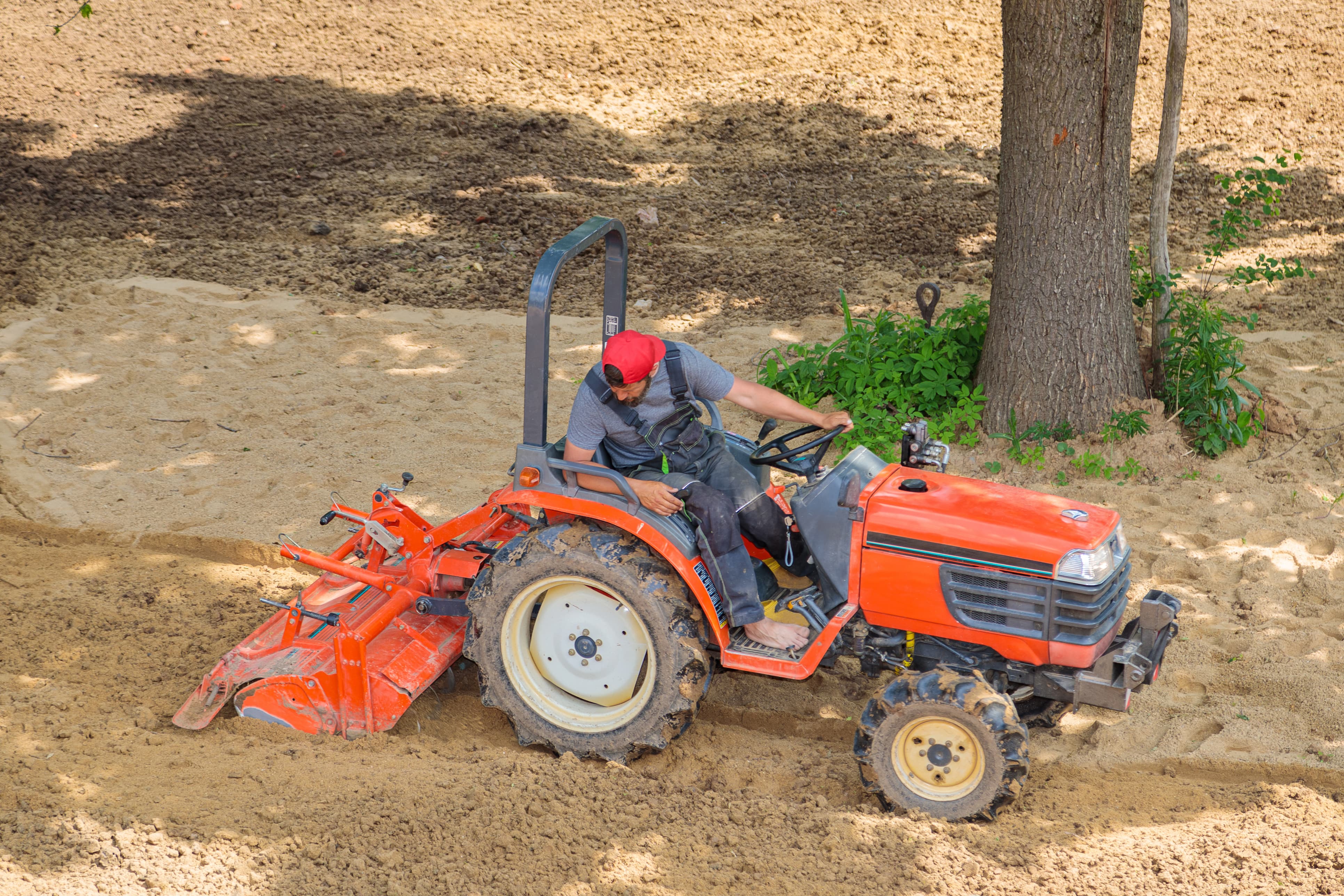
Hydraulic vs. Mechanical Disc Brakes? Heavy Equipment Needs Both
You’ll typically find two types of brakes on a piece of heavy equipment: hydraulic and mechanical. Why are both needed? Which brakes perform tasks that the other cannot?
One type of brake doesn’t...
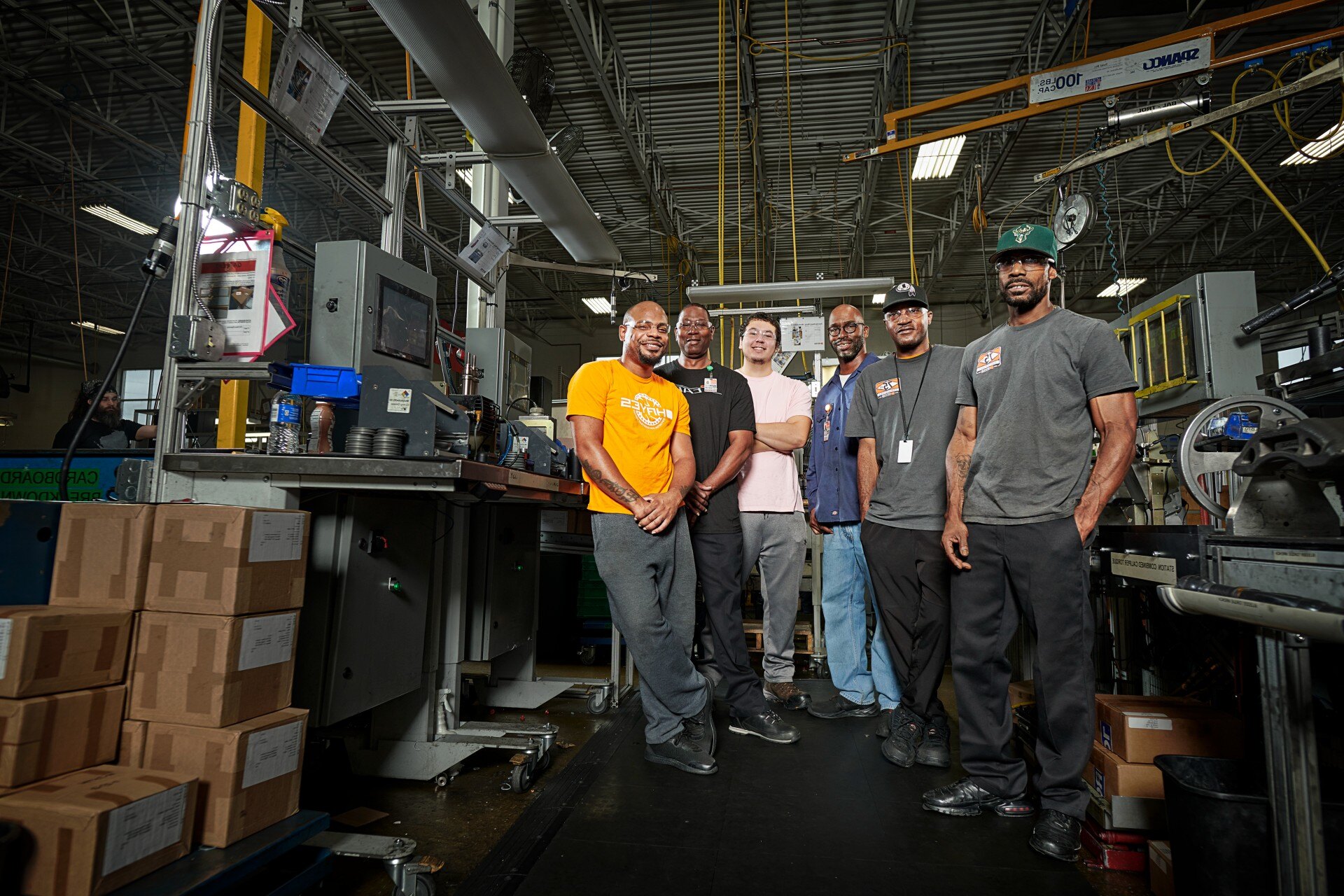
Maximize Performance & Minimize Costs: The Value of Expert-Led Custom Brake Development
When OEMs partner with brake system specialists early in the vehicle design and development process, they unlock key benefits—most notably, faster time-to-market and better cost management.
To...
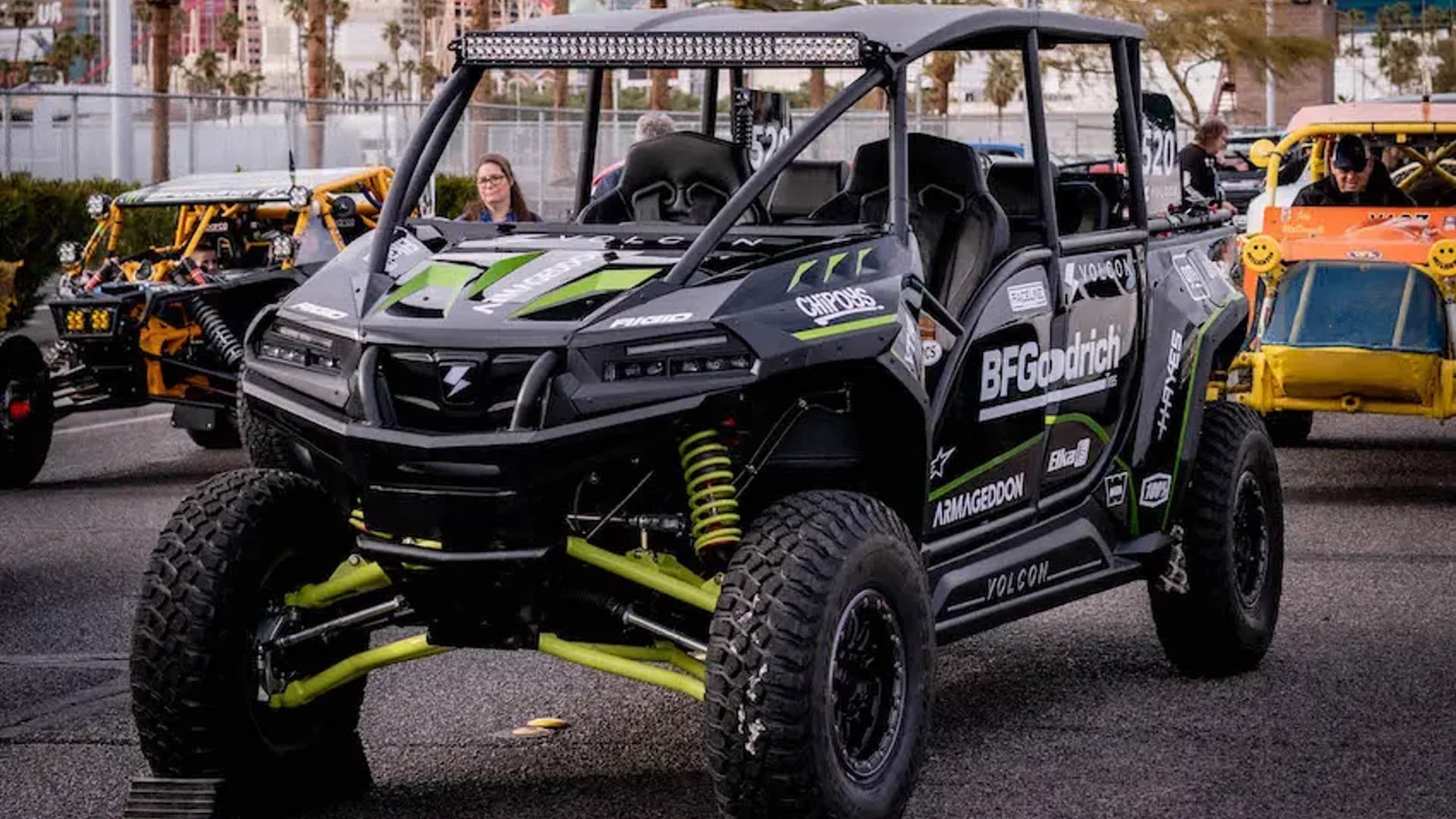
Electric Vehicles and Dry Disc Brakes: A Combination That Promotes Efficiency & Safety
Do electric vehicles (EVs) use the same brake systems as conventional vehicles? Yes and no.
Some light EVs – ebikes and scooters, for example – rely primarily on regenerative braking systems. These...