How to Prevent 5 Common Failures in Dry Disc Brakes
Share this
The best way to solve a problem? Prevent it from happening in the first place.
While your customers will always be responsible for routinely inspecting and maintaining their brakes throughout ownership, you can give them a head start by equipping your vehicles with high-quality dry disc brake systems that won’t become headaches.
Dry disc brakes have become the standard in many industries — heavy equipment (e.g., construction and agriculture vehicles), ATVs, UTVs, turf care vehicles, motorcycles, passenger cars, and more.
Regardless of industry, OEMs can run into five common dry disc brake issues:
Before these issues cause significant problems for your operations or your customers, you can address them in the early stages of design and engineering.
1. Overheating
Excessive friction is frequently the cause of overheating, but environmental or installation factors may also be involved. Whether caused by too much force from an operator’s poor braking techniques, exposure to temperatures beyond tolerance, or misaligned components, overheating is a serious issue that could lead to more complications.
How to Address During Design/Engineering
While you can’t do anything about operator error at this point, you and your brake manufacturer can collaborate early in the development stage to ensure that functionality and design are aligned and that every piece works with the others.
It’s also important to conduct dynamometer and other brake tests to find the heat limits of all components, which can then be noted in operation manuals and other materials.
2. Brake Pad Wear & Tear
Normal levels of wear and tear are expected, but brake pads shouldn’t be unevenly gripping the rotor or completely worn down before the end of their lifespan.
How to Address During Design/Engineering
First, make sure the pads are thick and durable enough to withstand the anticipated brake force. Account for friction and heat tolerance, compression strength, material density, and resistance to cracking. Then, consider the elements that work directly with the brake pads.
Pad springs retract brake pads to create quick disengagement and equal force distribution. However, double-acting pad springs, such as those found with our Sovren SD35 hydraulic brake, can boost overall functionality.
3. Brake Rotor Damage
Like brake pads, brake rotors/discs undergo typical wear and tear but might also experience misuse, malfunctions, or debris. Premature warping, scoring, and cracking are all possible.
How to Address During Design/Engineering
Starting with strong materials is a crucial first step in developing rotors that will last. Don’t look for the cheapest parts, as quality will likely be subpar. Once the proper materials are in place, tolerance testing finds the limitations that can be noted to help prevent operation errors.
4. Noise
Disc brake noise is a common issue when brakes aren’t installed correctly, when there’s dust/debris buildup, components are worn out, or the brakes are carrying too much weight.
How to Address During Design/Engineering
Along with using high-quality parts, make sure those parts are properly fitted. Pads, calipers, cylinders, rotors — every component must be designed and optimized to work with precision, eliminate excessive vibration, and maintain consistent performance.
5. Contamination
Some vehicles’ operating conditions can contaminate brake systems. Agriculture and construction vehicles are especially susceptible, since they often operate in muddy or rocky environments.
How to Address During Design/Engineering
Intricate elements that require optimum conditions to operate, such as the automotive pins within hydraulic brakes, must be located inside a durable enclosure to protect against dust and debris. For instance, Hayes’ SAHR actuator permanently seals springs inside a corrosion-resistant chamber specifically to prevent contamination.
In cold climates where roads are treated with salt after snowstorms, dump trucks, tractors, and other vehicles that drive on salted surfaces benefit from zinc coating on specific brake components for added protection against corrosion.
Further Reading: Dry Disc Brakes vs. Wet Disc Brakes
The Right Brakes, the Right People
High-quality parts, design, and engineering are essential considerations for equipping your vehicles with the brakes they need.
Depending on the applications, some of these problems are more significant than others. A riding lawn mower won’t have to deal with the kinds of weight loads wheel loaders face; a farmer’s tractor won’t be moving at the same speeds as motorcycles on nearby highways. It’s vital that every brake system is designed specifically for its vehicles.
To promote the optimal performance and longevity of the brakes you include with your vehicles, find the right brake manufacturing partner early in development. If you’re ready to collaborate on exceptional brake designs, let’s have a conversation.
Subscribe to our blog!
Related blogs
Section Intro
Help visitors get the basic idea within a few seconds, so they understand what this section is about.

Dry Disc Brakes: How Engineering Impacts Performance & Safety
Dry disc braking systems, when they came into widespread use decades ago, represented a significant improvement over drum brakes. They’ve been used ever since in everything from mountain bikes to...
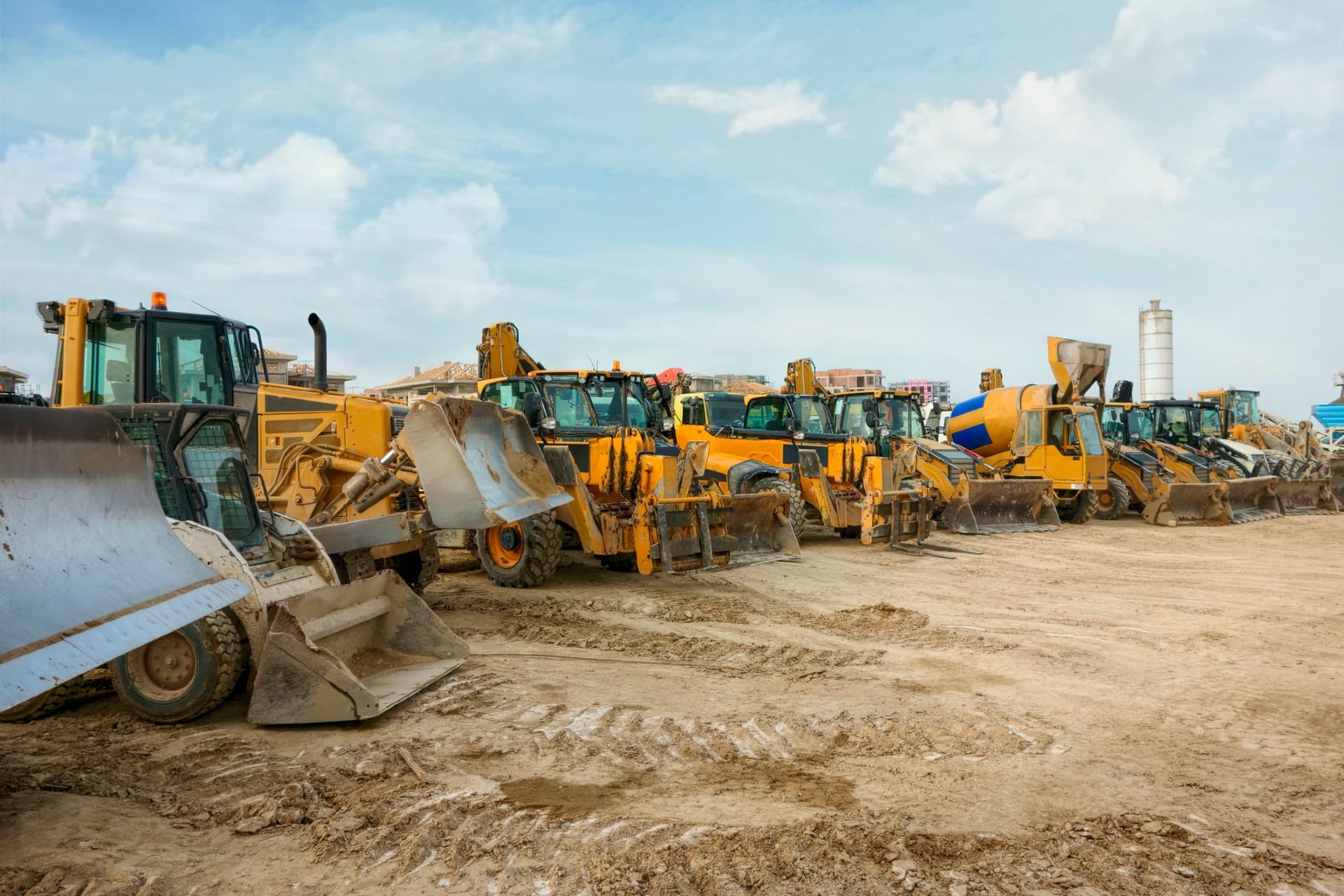
7 Reasons for Brake Failure in Heavy Equipment and How to Avoid Them
Brakes must work, but that doesn’t mean they always do. And when they don’t work when needed in heavy equipment, that puts operations behind schedule and risks profit loss.
In most cases, brake...
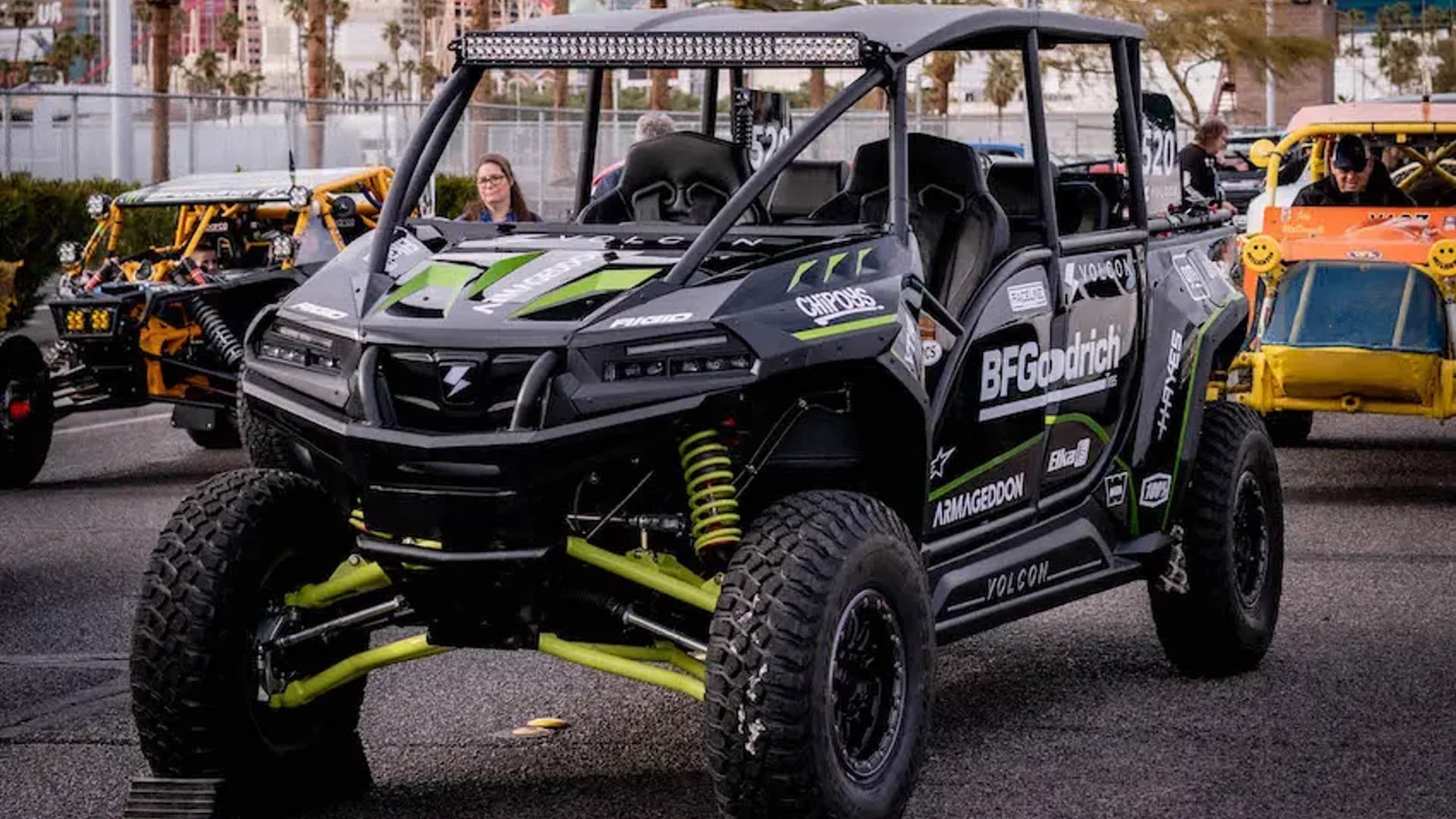
Electric Vehicles and Dry Disc Brakes: A Combination That Promotes Efficiency & Safety
Do electric vehicles (EVs) use the same brake systems as conventional vehicles? Yes and no.
Some light EVs – ebikes and scooters, for example – rely primarily on regenerative braking systems. These...