Spring Applied Hydraulic Release Brake Actuator: 4 Benefits for the Construction Industry
Share this
In 1990, Hayes Performance Systems patented its Spring Applied Hydraulic Release, or SAHR, brake actuator (initially called the Spring Applied/Pressure Release Emergency Brake Actuator) as a fail-safe option for construction vehicles. The SAHR has evolved over time, but has always been a remarkably reliable – and critical – component of heavy equipment braking systems.
Let’s take a look at how the SAHR works, and its benefits to the construction industry.
How the SAHR Works in Construction Vehicles
Very simply, when a vehicle’s hydraulic component fails, the SAHR “steps in” to stop it.
Some designs vary, but the SAHR that Hayes designed — and the general operation for many iterations — involves a large coil spring-loaded inside an 8-inch can. This spring constantly applies brake force, which is only released when hydraulic pressure counteracts the spring force. The SAHR ensures the brake engages even if pressure is lost.
The SAHR isn’t an entire brake but is ready for use in varying braking systems. In the construction industry, SAHR brake actuators are commonly used on equipment such as wheel loaders, telehandlers, and dump trucks.
Key Advantages of the SAHR Brake Actuator
Strength & Durability
Hayes’ current SAHR brake actuator handles continuous system pressures of up to 3,675 PSI.
Safely sealed inside the corrosion-resistant chamber, the spring absorbs incredible force and can handle almost any condition — rain or shine, hot or cold. When drivers engage the brake, the SAHR ensures that they only need to apply “normal” force in every instance; in other words, the operator doesn’t have to pull harder against heavier resistance.
Constant Force
The amount of force applied to a brake can be inconsistent, based upon the type of caliper and a human element that varies between operators. Use of a SAHR to actuate the brake eliminates these issues.
Operator Inconsistency
In a manual configuration, how much force and how far the lever moves can be traced back to the operator. For example, one person may pull less than another, putting less force to the brake rotor. This can put the vehicle at risk of rolling away instead of remaining safely parked.
Manual Adjustments
Some brakes or calipers require manual adjustment to reposition the lever for the caliper to work effectively. Adjustments may need to be repeated multiple times in a single service appointment to get the correct settings.
SAHR Solution
The SAHR eliminates these issues by working in conjunction with the brake caliper. The SAHR provides a constant, stable force to the brake caliper due to its large internal spring(s). The amount of force is preset and calculated by the brake manufacturer and the vehicle OEM. That constant force ensures that there is no variability of force to the brake rotor and the vehicle will remain safely parked.
Space Saving
The Hayes SAHR components are conveniently packed and sealed inside an 8-inch-long chamber. This compact unit saves space that manufacturers can allocate to other essential vehicle features.
Why SAHR Features Are Important for Construction Vehicles
The SAHR actuator performs reliably on construction sites, where demands on a vehicle are rigorous — typically, massive loads are being hauled across uneven terrain, sometimes in extreme weather conditions. Given the hazardous nature of construction, a fail-safe mechanism for the brakes is critical for worker safety.
Because it was designed to require little maintenance, the SAHR actuator saves time and resources that can instead be applied to completing the construction project.
Speak to the Brake Experts
As the originators of the SAHR actuator, the expert engineers at Hayes are the authorities on these crucial brake components. Reach out to our team to learn how the SAHR can be integrated into your vehicle design plans.
Subscribe to our blog!
Related blogs
Section Intro
Help visitors get the basic idea within a few seconds, so they understand what this section is about.
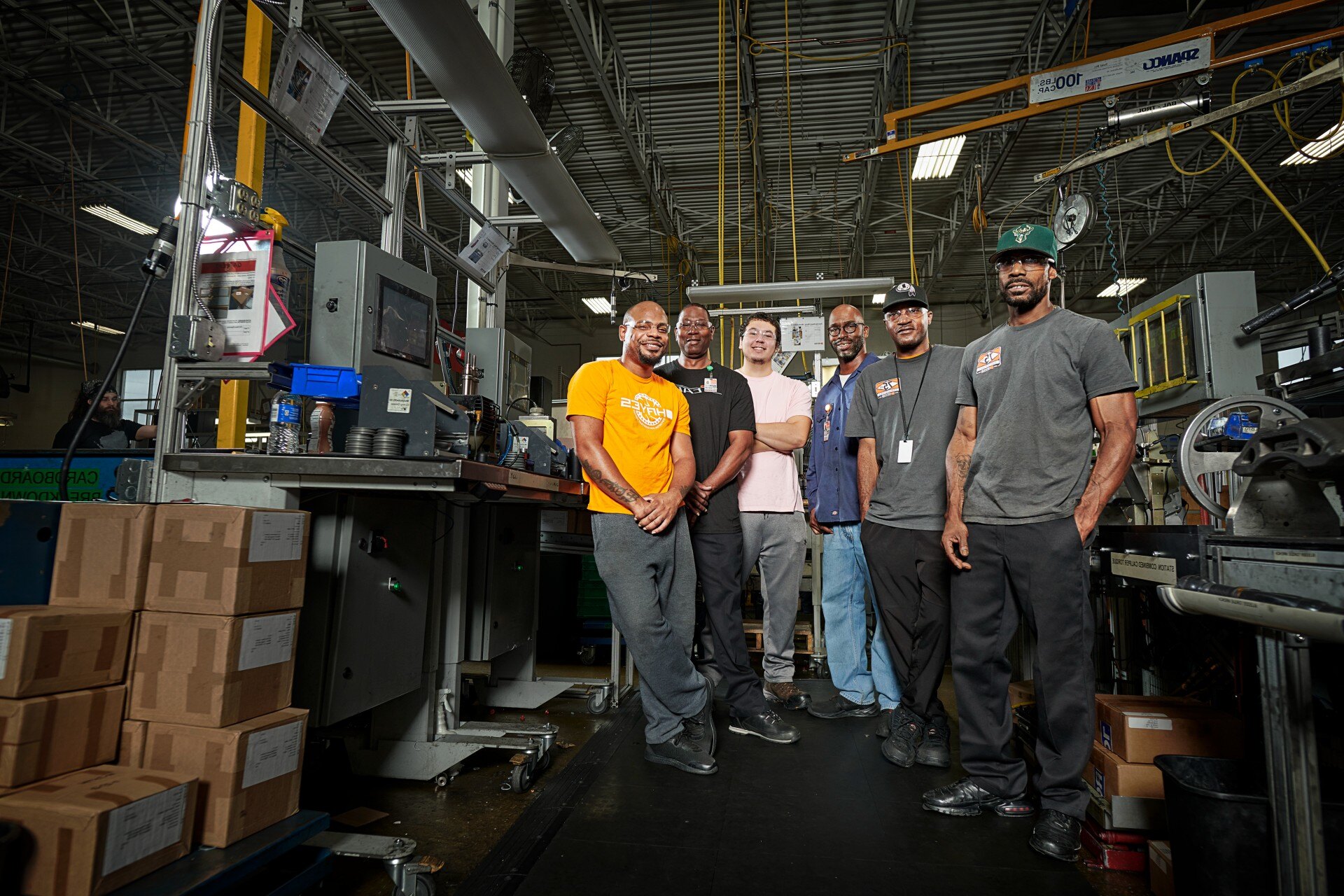
Maximize Performance & Minimize Costs: The Value of Expert-Led Custom Brake Development
When OEMs partner with brake system specialists early in the vehicle design and development process, they unlock key benefits—most notably, faster time-to-market and better cost management.
To...
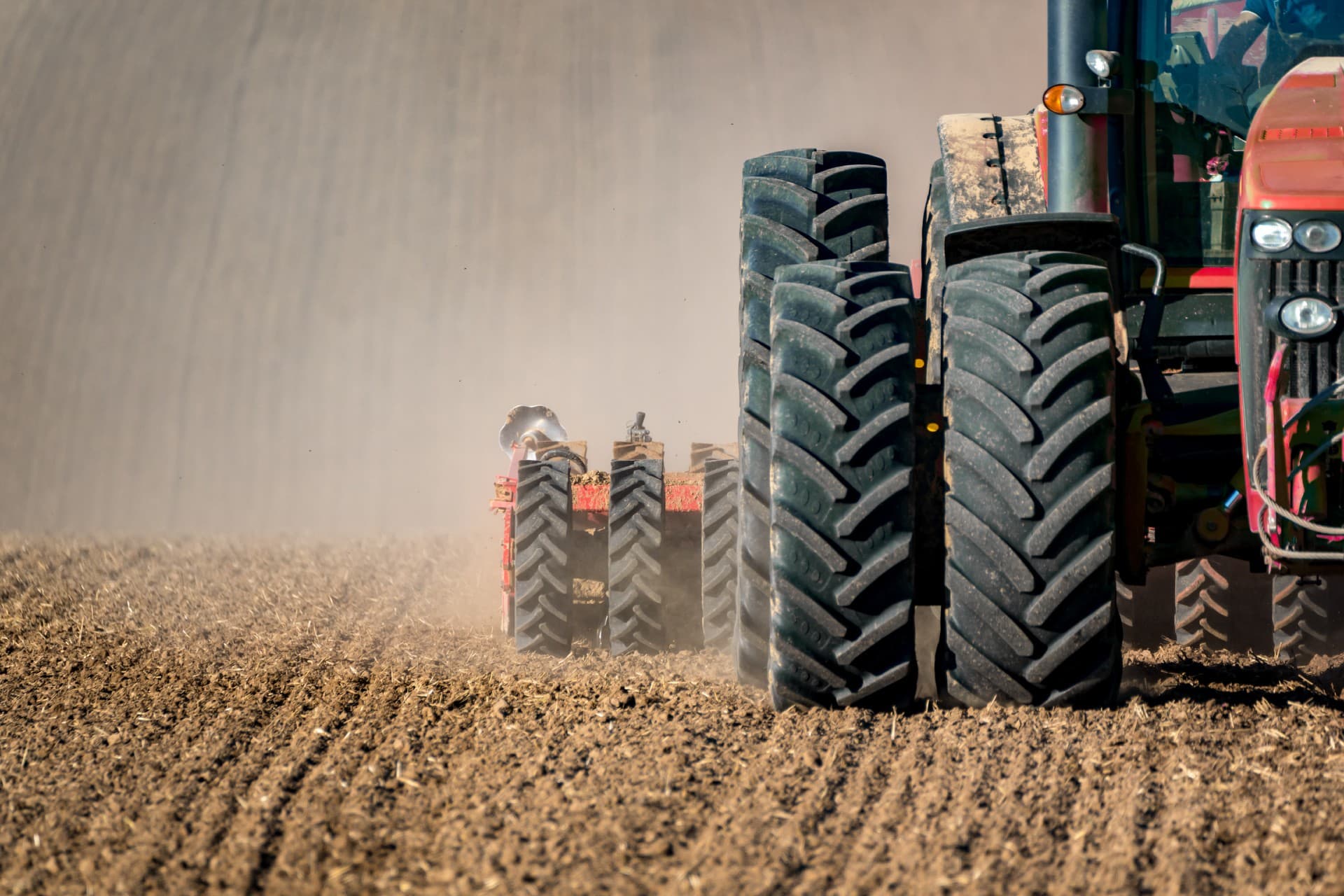
Dry Disc Brakes vs. Wet Disc Brakes
Brakes are brakes, right? Not exactly. Two of the most common braking systems — dry disc brakes and wet disc brakes — operate in unique ways and aren’t necessarily interchangeable.
Let's explore the...

Dry Disc Brakes: How Engineering Impacts Performance & Safety
Dry disc braking systems, when they came into widespread use decades ago, represented a significant improvement over drum brakes. They’ve been used ever since in everything from mountain bikes to...