OUR PRODUCT
ENGINEERING CAPABILITIES
Driven by a desire to innovate and exceed expectations, the Hayes engineering team is proud to have a breadth of competencies, experiences, and capabilities that are unique within the industry.
Our Team
It starts with the right people.
.png?width=847&height=785&name=_K4I1488%201(1).png)
Unparalleled Experience
Knowledge and wisdom are on our side. Our engineers average nearly 10 years of experience, and each team member has brought to Hayes — or developed from within — brake-specific expertise and application know-how.
What’s more, our engineers are immersed in the markets we serve, living and breathing them even outside of work hours. Many are avid riders, drivers, or racers, and all have a passion for ensuring we make the best products in the business.
Nurturing Our Future
We’re always on the lookout for brilliant minds. Our internship program ensures that talent is identified, nurtured, promoted, and retained. It’s been so successful that past interns from this program now represent roles in engineering, sales, product management leadership, and even senior leadership.
The Hayes team also boasts certified Six Sigma Greenbelts, leadership, and program management curriculum graduates, plus several team members who are active in professional consortiums.
A Collaborative Mindset
Our success comes from respect and collaboration. We recognize and appreciate the knowledge and experience of others, and we work tirelessly with one another — regardless of department — while working with customers to develop the right solutions the right way.
our method
“Build, test, race, repeat.”
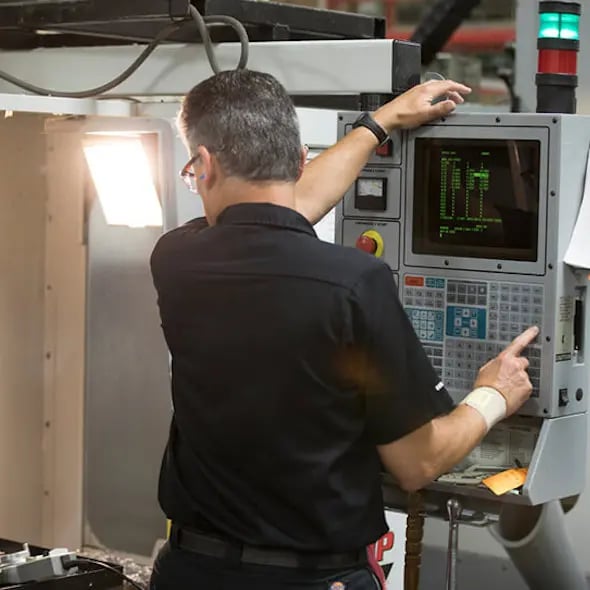
Engineering & Testing
Hayes employs top-tier engineering methods and test procedures aimed at ensuring quality, consistency, transparency, and quick issue resolution. Our Research & Development (R&D) process is tailored to support a fast pace, leading to the learning cycle mantra above.
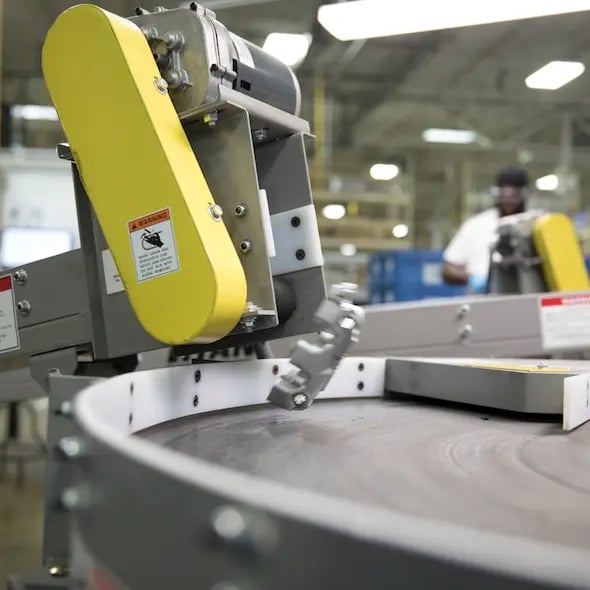
State-of-the-Art Technology
Our sophisticated tools include:
- 3D modeling, multi-physics analysis, and vibration analysis software
- Fully staffed lab with cloud-based management software
- Workflow management tied directly to departmental performance metrics
- Key equipment with monitoring and control to allow 24/7 test support and preventative maintenance
- Vehicle proving ground for on-road and off-road applications
- Methods to support bicycles, wheel loaders, and everything in between
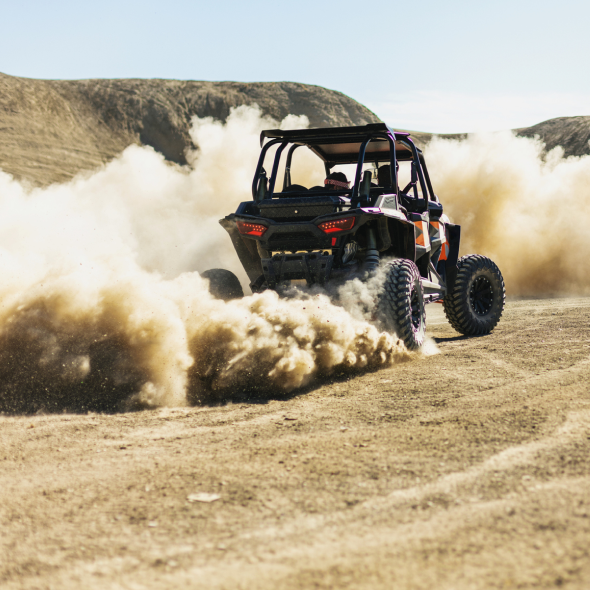
On-Track Testing
Meeting exacting specs is one of the Hayes engineering team’s biggest motivators — whether it’s from government vehicle applications, high-performance race vehicles, or anything in between. And speaking of races, the Hayes R&D team actually uses the racing environment to test products under rigorous demands.
Engineers at Hayes have the exciting and enviable opportunity to directly interact with customers and competitive athletes in multiple racing disciplines. In some cases, Hayes engineers are embedded on professional race team crews, while others are able to attend events and address questions from race crews and get direct feedback on the product. This valuable input makes its way back to the development team for any necessary product improvements or new opportunities.
Hayes R&D currently partners with teams that participate in:
- MotoAmerica, Superbike Class
- Bagger Racing League
- Championship Snocross
- Short Course UTV Racing
- Cross Country Snowmobile
Key Partnerships
It starts with the right people.
While most lab testing is completed at our engineering headquarters, we maintain multi-year key partnerships with local and regional specialized test labs to ensure we have capacities and capabilities at any time to test products.
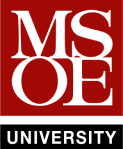
Hayes is proud to partner with the Milwaukee School of Engineering (MSOE) — a leading engineering school in the Midwest — through their Rapid Prototype Consortium, giving our team insight and access to the latest additive and scanning technologies.
Hayes partners with world-famous Road America near Elkhart Lake, Wisconsin, for the purpose of the on-road and off-road testing of vehicles. We operate there from our private test garage, which is a short 45-minute drive from our engineering headquarters in Mequon, Wisconsin.
The Right Tools for the Job
It starts with the right people.
.png?width=712&height=608&name=_K4I1488%201%20(4).png)
Analytical Tools & Methods
- CAD and basic FEA stress and deflection using PTC Creo
- Advanced FEA (multi-physics, non-linear, fatigue) using ANSYS
- Standardized predictive tools for brake system sizing, bolted joints, tolerance stacks
- Product Data Management using PTC Windchill platform (PDMLink) – configuration management for both R&D and production environments
- ReliaSoft XFMEA software
- Clarivate Derwent Innovation patent search software
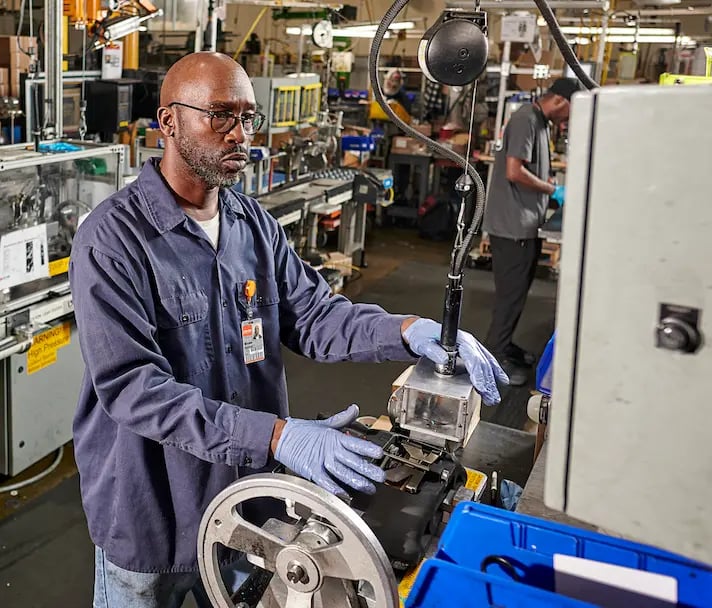
Physical Tools & Methods
- Custom 100 HP brake dynamometer with ProLINK controls, up to 1850 ft-lbs, 235 mph
- Fleet of 20+ vehicles, Hayes and customer-owned, covering a wide range of markets
- B&K LDS V850 Vibration test system
- Tekscan pressure mapping and force measurement
- ESPEC environmental chambers
- Independent pumps supporting a wide range of fluid, pressure, and flow requirements for performance and life testing
- Digital microscope with measurement and capture capabilities
- DC drive torque-angle for bolted joint development and verification, programmable custom, customer, and production torque profiles
- ABS and ESC systems simulation for master cylinder performance and life
- Dedicated proto-build area in engineering lab where engineers control and facilitate key builds until production equipment is online
Want to learn more about our methods and capabilities ahead of outfitting your vehicles with our brake systems? We’d love to talk! Connect with us today and we’ll be in touch soon.