Dry Disc Brakes: How Engineering Impacts Performance & Safety
Share this
Dry disc braking systems, when they came into widespread use decades ago, represented a significant improvement over drum brakes. They’ve been used ever since in everything from mountain bikes to heavy-duty military trucks. They’re the most common type of braking system today, primarily because they’re simple, efficient, and reliable.
In this article we’ll examine how dry disc brakes function, and the engineering involved in ensuring that their performance aligns with the vehicle’s requirements.
What’s Involved In a Dry Disc Brake?
Dry disc brakes are made up of four primary parts:
- a brake disc (or rotor) that’s attached to the wheel hub
- a caliper that houses brake pads on either side of the disc
- brake pads that are pressed against the disc
- the actuation mechanism that executes the braking process
- a master cylinder that converts mechanical force to hydraulic pressure (the inverse of what the caliper does)
The disc. The disc is the flat, round component that rotates with the wheel. This is the surface onto which the brake pads clamp, creating friction that slows and stops the vehicle.
The calipers. The caliper straddles the disc and contains pistons and brake pads. The pistons are what press the brake pads against the disc to create the friction, converting hydraulic pressure to mechanical force, which equates to clamp force on the brake disc. Calipers can be fixed (with pistons on both sides) or floating (with pistons only on one side, moving in and out as the brakes are applied). Fixed calipers provide more even braking force and are used in high-performance vehicles while floating calipers are ideal for everyday use and are found in many passenger vehicles.
The brake pads. Brake pads are attached to a metal backing plate and positioned on either side of the disc. The pads are pressed against the disc to create friction and slow the rotation of the disc and the wheel.
The actuation mechanism. The actuation mechanism transmits the driver's input from the brake pedal to the calipers (when the driver presses the brake pedal, hydraulic pressure forces the caliper to clamp the brake pads against the disc). The system is made up of the brake pedal and the master cylinder.
How Dry Disc Brake Components Work Together
Now that you know what makes up a dry disc brake, let’s talk about how these components interact to provide safe, effective braking.
The first step in the process begins when the driver presses the brake pedal. The force the driver inputs to the brake pedal is transferred to the master cylinder. Then:
- The master cylinder converts the mechanical force from the brake pedal into hydraulic pressure
- The hydraulic pressure is transmitted through the brake lines to the brake calipers and distributed to all brakes in the system
- The hydraulic pressure in the brake lines acts on the caliper pistons
- The caliper pistons push the brake pads against the rotating disc
- As the brake pads press against the disc, friction between the brake pads and the disc slows the wheel
Once the brake pedal is released, the hydraulic pressure in the brake lines decreases, the pistons retract, and the brake pads move away from the disc, allowing the wheel to rotate freely again.
By working together, the disc brake’s components provide reliable braking critical for safety and performance.
RELATED: Learn how material choice affects brake performance in Powersports
How Engineers Select Disc Brake Materials
There are several material characteristics braking system engineers consider as they determine which will be used to manufacture their dry disc brakes. The material options are aluminum, cast iron, stainless steel, and steel, and each has benefits that make them ideally suited for different vehicle types and uses.
- Heat absorption and dissipation: The material should absorb and store heat without degrading, dissipate heat quickly to prevent overheating and “brake fade,” and have a low thermal expansion rate to reduce the risk of warping
- Friction: The material should provide consistent performance across a range of temperatures and conditions and resist wear to maintain performance and prolong the life of brake components
- Strength: The material should withstand the forces applied during braking, maintain structural integrity, and resist the stress of repetitive braking cycles
- Durability and longevity: The material should handle continuous use without degrading and resist environmental factors like moisture and road salt
- Weight: Lighter materials help reduce overall vehicle weight and improve fuel efficiency
- Cost and manufacturability: The material cost should be appropriate for the vehicle type and compatible with manufacturing processes
- Noise and vibration: The material should minimize noise and dampen vibration to maintain smooth operation
With all these factors at play, the brake systems engineer is essentially doing a balancing act, weighing the pros and cons of each material and how they impact performance. In the process, they also have to consider the vehicle and its specific use, environmental conditions, and the material’s cost.
RELATED: Learn how to improve disc brake performance
Brake systems engineers will compare these main material characteristics:
Weight | Cost | Performance | Durability | |
Aluminum | Lightweight | High | Good thermal conductivity; moderate strength | Corrosion-resistant |
Cast Iron | Heaviest of these options | Moderate | Good thermal conductivity; strong | Wear-resistant; can tolerate high temperatures; requires rust protection |
Stainless Steel | Heavier than aluminum, lighter than cast iron | High | Excellent corrosion resistance and strength | High durability; corrosion-resistant |
Steel | Heavier than aluminum, lighter than cast iron | Low | Very strong; heat resistant | Extremely durable; requires rust protection |
While aluminum is often more expensive than other materials, its performance, durability, and light weight make it ideal for many vehicle brake systems. Cast iron is a cost-effective and reliable option, while stainless steel and steel offer a good mix of performance, weight, and durability.
As mechanically “simple” as dry disc brakes are, engineering them requires a deep understanding of all material options (including the many different alloys of each metal), and how each affects brake and vehicle performance. Our experts evaluate all the factors involved in identifying the most appropriate materials for the vehicle and its use. In addition to the listed above, we also take into account manufacturing and/or processing methods that could impact the material performance. Friction material type, too, plays a big role in disc material selection and is determined by the vehicle’s use and performance goals, and any relevant regulations.
You can see that material selection is rather complicated, and critically important. Rest assured that the team at Hayes has the engineering expertise required to specify the materials best suited for the performance and safety of your vehicle. Don’t compromise your next project – insist on brakes engineered and tested for performance excellence.
Subscribe to our blog!
Related blogs
Section Intro
Help visitors get the basic idea within a few seconds, so they understand what this section is about.
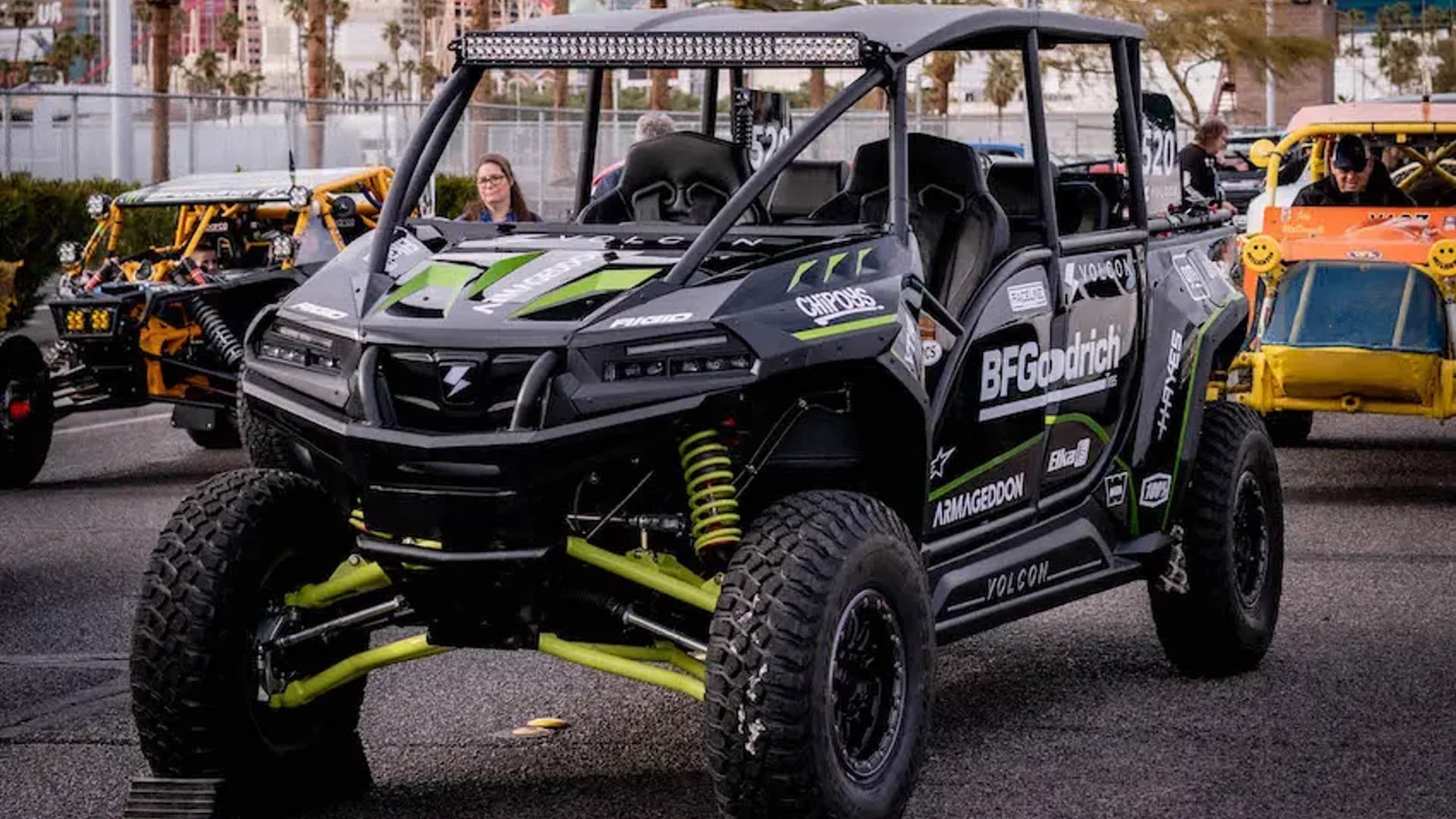
Electric Vehicles and Dry Disc Brakes: A Combination That Promotes Efficiency & Safety
Do electric vehicles (EVs) use the same brake systems as conventional vehicles? Yes and no.
Some light EVs – ebikes and scooters, for example – rely primarily on regenerative braking systems. These...

How to Prevent 5 Common Failures in Dry Disc Brakes
The best way to solve a problem? Prevent it from happening in the first place.
While your customers will always be responsible for routinely inspecting and maintaining their brakes throughout...
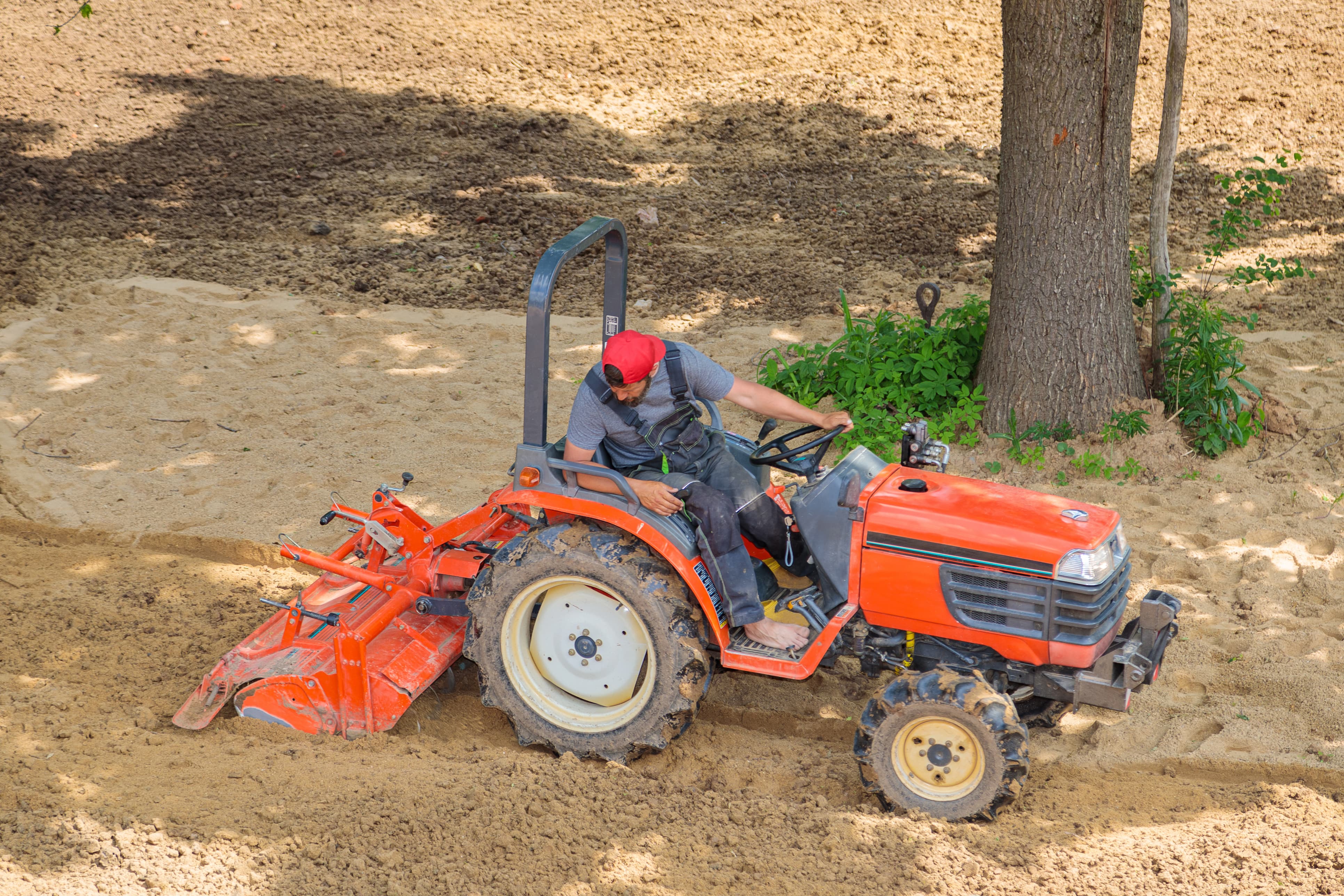
Hydraulic vs. Mechanical Disc Brakes? Heavy Equipment Needs Both
You’ll typically find two types of brakes on a piece of heavy equipment: hydraulic and mechanical. Why are both needed? Which brakes perform tasks that the other cannot?
One type of brake doesn’t...